Uni Grouts GP 65 is a premixed cement based, non-ferrous, non-shrink grout, exhibiting good flow characteristics. This economical performance grout offers the advantage of low water requirements and medium to high compressive strengths. Uni Grouts GP 65 should be specified for general purpose construction site applications where the major emphasis is on ease of application. Uni Grouts GP 65 is supplied ready-touse as a dry powdered product requiring only the addition of water to be used for a wide range of applications.
Uni Grouts GP 65 produces high early and ultimate strengths without intermediate or latent shrinkage. Uni Grouts GP 65 remains stable without failure from compressive loading, impact, lateral thrusts, high heat or continuous vibration. Plastic settlement and shrinkage are prevented by the shrinkage compensated mix design. Low mixing water demand results in the hardened grout giving good freeze-thaw stability, low water absorption plus resistance to oil, sea water and mild alkali attack. The grout is chloride free, can be safely used in contact with steel and can be placed in section thicknesses of 10mm up to 100mm.
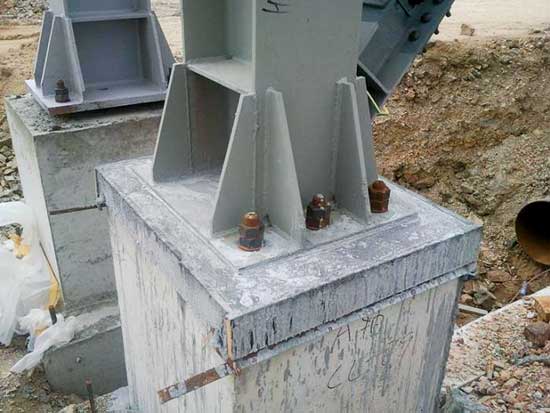
Uni Grouts GP 65 Uses
Uni Grouts GP 65 is used for precision grouting where it is essential to withstand static and dynamic loads. Typical applications would be the grouting of base plates of turbines, compressors, boiler feed pumps etc., It can also be used for anchoring a wide range of fixings. These include masts, anchor bolts and fence posts.
Uni Grouts GP 65 Advantages
- Prepacked, In factory ensures consistency in supply requires addition of water to develop a free flow, non shrinking and high strength gaining grout.
- Material shrinkage is offset by expansion during green condition and later on by maintain original volume.
- Self leveling by nature.
- Easy placement and filling of under base of machinery.
- Contains no chlorides, or corrosive ingredients.
- Similar appearance to concrete
Uni Grouts GP 65 Typical Properties
General purpose, non-shrink, free flow cementitious grout
Compressive Strength (BS 1881 : Part 116,1983 & ASTM C 1107) @ w/p ratio 0.18 (flowable), w/p ratio 0.16 (Pourable)
AGE IN DAYS | COMPRESSIVE STRENGTH IN N/mm² | |
---|---|---|
Flowable W/P=0.18 | Pourable W/P=0.16 | |
1 | 24 N/mm² | 27 N/mm² |
3 | 40 N/mm² | 50 N/mm² |
7 | 55 N/mm² | 65 N/mm² |
28 | 65 N/mm² | 75 N/mm² |
Flexural Strength (BS 4551, 1998)
AGE IN DAYS | COMPRESSIVE STRENGTH IN N/mm² Flowable W/P=0.19 |
---|---|
1 | 2.5 N/mm² |
3 | 7 N/mm² |
7 | 9 N/mm² |
28 | 10 N/mm² |
Unrestrained expansion | 1 to 4% |
0 Consistency Life | 20 minutes @ 30 C |
3 Density | 2000 kg/m |
Initial Setting Time | Approx. 5 hrs. |
Flow on Flow Table | 17 to 24 cms. |
Note : Cubes cast were kept under resistant before testing to simulate site condition. Size of the cubes used 70.6mm x 70.6mm x 70.6mm tested at 300C.
Instruction for Uni Grouts GP 65 Use
General purpose, non-shrink, free flow cementitious grout
Surface Preparation
All surfaces must be clean, sound and free from dust, ice, oils, grease and other surface contaminants such as curing membranes and form release agents etc. Bolt holes and fixing pockets should be free of dirt and debris by air blasting. For maximum bond, surfaces should be abraded or roughened, preferably by mechanical means such as needle gun, grit blasting, grinding etc. All prepared surfaces must be saturated with water several hours prior to grouting, ensuring it is free of any surface water or puddles.
Formwork
Mixing
Placing
Uni Grouts GP 65 can be placed in thicknesses up to 100mm in a single pour when used as an under plate grout. For thicker sections it is necessary to fill out Uni Grouts GP 65 grout with well graded silt free aggregate to minimize heat buildup. Typically a 10mm aggregate is suitable. 50 - 100% aggregate weight of Uni Grouts GP 65 can be added. Any bolt pockets must be grouted prior to grouting between the substrate and the base plate.